耐火喷涂料
- 发布人:管理员
- 发布时间:2013-08-15
- 浏览量:2857
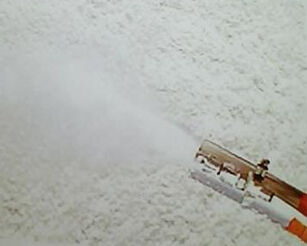
定义:用喷枪或泵送将耐火材料预混料喷射到受喷面上,即用喷涂方法施工的材料称为耐火喷涂料。
1耐火喷涂料的分类:
按喷涂方法分为湿法、干法和火焰法3类;按受喷面接受物料时的状态又分为冷物料喷涂法和熔融物料喷涂法。
1.1湿法:
湿法喷涂是指耐火喷涂料加水或液体结合剂后喷射到受喷洒面上的。根据加水或液体结合剂的顺序及其用量的不同,又划分为泥浆法、湿式法、半干法和假干法4种。两种方法混合使用的,则称为混合法。
泥浆法是先将耐火预混料搅拌成泥浆后再喷涂,主要用于热喷补炉衬;湿式法是将耐火预混料加水或液体结合剂搅拌成泵送泥料后再喷涂,可筑炉造衬或进行补炉,是近十年来开发的新施工方法,其优点是无粉尘污染和附着率高;半干法是先将耐火预混料加少量的水搅拌润湿均匀,输送到喷嘴处再加余下的水后进行喷涂;假干法是将耐火预混料通过搅拌机混匀,再输送到喷嘴处加水后进行喷涂。
1.2干法:
干法喷涂是将耐火预混料通过喷嘴直接喷射到受喷面上的,主要用于补炉。镁质类耐火喷涂料基本上是采用该法进行补炉的,故也称为镁质类耐火喷补料。
1.3火焰法:
火焰法喷涂是用氧气将预混合好的耐火喷涂料输送到喷嘴处与可燃气体或固体燃料相遇一起喷出,可燃气体或固体燃料燃烧,喷涂料在火焰中行进并熔融成塑态射到受喷面上。可燃气体有丙烷和煤油等,在喷嘴处加入喷出。可燃物料有焦粉等,先与耐火喷涂料预混合。该法主要用于热喷补炉衬,对原衬损伤少,喷涂层易烧结,使用寿命长,但成本较高。另外,用等离子枪将耐火预混料熔融或半熔融后喷射到受喷面上,也归属该类方法。
耐火喷涂料的材料组成,与同品种的耐火浇注料基本相似,凝结硬化机理和高温下的物理化学变化也基本类同,故一般不再赘述。其区别是耐火骨料临界粒径较小,一般为3~5mm,耐火粉料、微粉和结合剂的合用量较多,一般为33%~45%。为提高喷涂料的输送性、附着性和烧结性,一般应添加增塑剂、增黏剂和烧结剂。同时,喷射机种类、施工工艺参数、受喷体状态和使用条件等环节,也是影响喷涂层质量的重要因素。所以,应精心调整材料,合理确定配比和机型,严格控制喷涂工艺。
镁质类耐火喷涂料分为重质和轻质两类,应用最多的是前者,即耐火喷补料。该料在转炉、电炉、钢包及二次精炼炉等热工设备上,得到了广泛应用,获得了良好的使用效果。
2耐火喷涂料:
镁质类耐火喷涂料主要用于修补炉衬。该料按材质分为镁质、镁铝质、镁钙质和镁尖晶石质等喷补料;按施工方法分为干法和半干法等喷补料;按使用部位分为转炉、电炉和钢包等耐火喷补料。
2.1转炉耐火喷补料:
转炉耐火喷补料分为镁质、镁白云石质、镁铬质和镁钙质等品种,其结合剂一般用硅酸钠、磷酸盐、焦油沥青和树脂等。同时掺加硼砂、膨润土和活性SiO2等外加剂,用量一般为1~3%。该类料可用半干法或干法喷涂,也可用人工投补,是提高转炉炉龄的一项重要措施。
转炉耐火喷补料的临界粒径为3mm时,其颗粒级配:3~1mm,30%~50%;1~0.15mm,30%~35%;<0.15mm,20%~40%;当临界粒径为5mm时,其颗粒级配:5~3mm,20%~35%;3~1mm,20%~30%;1~0.15mm,10%~15%;<0.15mm,20%~25%;当用人工投补时,可采用临界粒径为10mm的耐火投补料。耐火喷补料的临界粒径和颗粒级配,应根据喷涂机、喷涂工艺、旧炉衬的损毁情况及其工作条件而定。选择得当,能降低回弹率,即提高附着性,增加体积密度及其强度。耐火喷料的临界粒径和颗粒级配,是获得良好喷补层的关键。表1为炼钢转炉耐火喷补料的性能。
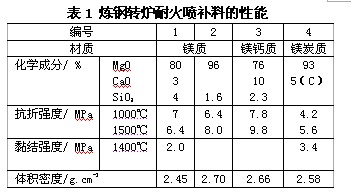
编号1和2的主体原料为高纯烧结镁砂。编号1掺加少量的消石灰,以便在高温下与磷酸盐结合剂形成高熔点的磷酸钙。编号3喷补料用的镁钙砂,临界粒径为3mm,>3mm的应小于5%,<0.074mm的应不小于25%,用磷酸盐作结合剂。编号4喷补料掺加少量的磷片石墨,并用酚醛树脂作结合剂。另外,在喷补料中常加矿化剂、增塑剂和烧结剂等,以便增强料与受喷面的黏结性和减少料的回弹率。
在转炉炼钢过程中,其炉衬喷补分为预防性喷补和维修性喷补两种。前者在转炉使用到中期,每隔3~5炉喷补1次,后者当炉衬损毁时即进行喷补。在炼钢转炉的吨钢耐火材料消耗中,喷补料的消耗约占1/4。目前,转炉炉衬修补普遍采用溅渣护炉技术,其炉龄达1万次以上。
在混铁炉前墙和出铁口两侧相交处,采用磷酸盐镁钙砂耐火喷补料喷补,喷补层厚度为200mm~250mm,回弹率小于15%,一般使用30多天。岩相鉴定证明,在高温下生成了磷酸钙钠新的高温相,因此有较好的使用效果。
2.2电炉耐火喷补料:
随着超高功率电炉大型化、生产连续化、且高温高效操作,加剧了炉衬的损毁,耐火喷补料应运而生。
表2为电炉耐火喷补料的性能。编号1~3分别用烧结镁砂、电熔镁砂作耐火骨料和粉料,同时添加了镁钙砂粉,编号2掺加了白刚玉粉,编号3添加鳞片石墨粉。采用聚磷酸盐等材料作复合结合剂。编号4用镁钙砂作耐火骨料和部分粉料,主体粉料为电熔镁砂粉,用沥青粉(或树脂粉)与六偏磷酸钠作复合结合剂。上述材料中,都添加了少量的增塑剂、矿化剂和α-Al2O3 。该类材料在超高功率电炉的渣线区域和热点部位使用,喷补层厚度一般为20mm~100mm,镁炭质喷补料附着率为85%左右,其余的均大于90%,获得了良好的效果。
表2 电炉耐火喷补料的性能:

2.3精炼炉和钢包用耐火喷补料:
炉外精炼是将初炼的钢水转移到另一个容器(主要是钢包)中进行精炼的过程,也称二次冶金。其作用是洁净钢水,过程为搅拌钢水、真空脱气、升温、喷粉或喂丝等。炉外精炼分为常压下精炼和真空下精炼两类,其中又分若干方法。常压下精炼如钢包底吹氩气搅拌,提高脱氧效率,使捕集到的夹杂物上浮,达到钢水温度和成分的均匀。真空下精炼如VOD法即VOD炉由真空泵室顶部吹氧、底部吹氩搅拌脱气;利用VOD法原理,在RH装置上加氧枪精炼不锈钢,称为RH-OB法等。精炼热工设备的统称为精炼炉。
表3为精炼炉和钢包用耐火喷补料的性能。

编号1为VOD炉用的喷补料,采用MgO >95%的烧结镁砂和MgO >96%的电熔镁砂作耐火骨料和粉料,添加镁钙砂粉、α-Al2O3和硅微粉等,采用聚磷酸盐和硅酸盐等材料作结合剂;编号2为RH-OB炉用的镁钙质耐火喷补料,材料组成:烧结镁砂4~0.5mm为48%,电熔镁砂0.5~0mm为20%,镁白云石1~0mm为11%和<0.088mm为10%,<200目CaO材料为3%,α-Al2O3和 μf-SiO2含量为3%~4%,聚磷酸盐和硅酸钠粉复合结合剂用量为4%~6%。同时,掺加有机纤维0.05%~0.1%,增强耐火喷补料的黏附性,降低回弹损失,在加热过程中能起防爆作用;编号3为精炼钢包用耐火喷补料,采用MgO>90%烧结镁砂作耐火骨料,用MgO >96.5%的电熔镁砂作粉料,并添加α-Al2O3 、增塑剂和减水剂等,用复合微粉和氨基磺酸盐作结合剂,用量为3%左右。骨料临界粒径为3mm,骨料与粉料之比约为65:35;编号4和5为普通钢包用耐火喷补料,采用特级矾土熟料作耐火骨料和粉料,临界粒度5mm,添加μf-SiO2、α-Al2O3和软质黏土等材料。编号4用MgO>95%烧结镁砂粉为12%,用模数为2.8的硅酸钠粉作结合剂。编号5用烧结镁铝尖晶石作1~0mm的骨料和200目的粉料,并掺加少量的电熔镁砂粉,采用CA-70水泥作结合剂。
在VOD炉上喷补10mm~30mm厚的喷涂层,能使用2-3炉,最高5炉;在RH-OB炉上喷补料附着率>90%,其寿命为3-4次;在90t精炼钢包上喷补料厚度为20mm~50mm,平均使用5次,获得较大的经济效益;普通钢包喷补料材质应根据钢包衬材质而定,相同材质有利于使用。在钢包冷态喷补时,耐火喷补料用水量少些;当钢包内衬温度较高时,其用水量应多些。这样方可获得良好的喷涂层,以提高使用寿命。混铁矿、鱼雷罐和铁水包等热工设备,损毁时也可采用耐火喷补料进行喷补,延长使用寿命。
2.4中间包耐火喷涂料:
中间包工作衬用耐火喷涂料,分为重质和轻质两类,前者为半干法喷涂而后者为湿法喷涂。本节还简介了高铝质耐火喷涂料用泵送方法喷射其永久衬的情况。表4中间包耐火喷涂料的主要性能。

编号1采用MgO≥95%的烧结镁砂作耐火骨料,临界粒径为2mm,采用MgO>98%的电熔镁砂作粉料,用软质黏土作增塑剂和烧结剂,并添加了SiO2 >93%的硅微粉、α-Al2O3和纤维防爆剂。加入纤维能降低其体积密度和导热系数,增强中间包的保温效果。采用聚磷酸钠等材料作复合结合剂;编号2为轻质耐火喷涂料,主要采用镁砂、纸纤维、玻璃纤维、硅微粉、膨润土和外加剂配成的预混合料,并添加烷基磺酸盐发泡剂及其稳泡剂。在现场,加水搅拌均匀后进行湿法喷涂。喷涂后的工作衬与永入衬黏结牢固,自然养护到期后并烘烤,包壁和包底衬体,基本上没有发生裂纹现象;编号3 为低水泥高铝质耐火浇注料,作中间包永久衬。该衬系采用湿式泵送喷射施工的,用水量5.6%~6.5%,连续作业,衬体厚度可在30mm~900mm间任意控制,不流淌,无滑落和坍塌。其使用寿命比振动浇注料和自流浇注料的提高10%~30%。从表3-35中看出,低水泥高铝质耐火浇注料用湿式泵送喷射施工,其强度比振动施工时高30%~90%。该料也可称为泵送喷射料。