奥迪车身技术再突破 镁合金的应用比上代车型减重28%
- 发布人:管理员
- 发布时间:2017-05-25
- 浏览量:1254
2017年的7月11日,奥迪A8将在国内首发亮相。作为旗舰级轿车,它可是代表了奥迪科技的走向,这不奥迪可就发布了全新一代奥迪A8车体……
作为在乘用车上应用轻量化铝合金材料的先驱之一,奥迪的ASF(Audi Space Frame)车身结构可以追溯到23年前,而在这二十多年的发展中,已经有9台奥迪车被打上了ASF的烙印,而在今天的第十款ASF车身将属于全新一代奥迪A8(D5)。
凭借着ASF车身技术,奥迪算得上是车身轻量化的先行者。特别是在品牌旗舰A8车型上,ASF车身结构带来的轻量化优势有目共睹。在材料科学和生产工艺不断进步的今天,新车型势必会在前作的基础上进一步减重,已获得更好的操控特性及燃油经济性。然而,全新奥迪A8的车身结构却比现款车型增重了近50公斤,究竟是奥迪在轻量化技术方面遇到了瓶颈,还是有什么事情比减重更重要?
四种材料混合
全新一代的A8要打破铝合金车身结构的传统,第一次以四种复合材料打造,分别是铝、钢、镁、CFRP碳纤维复合材料,其中CFRP只占车身重量的1%,却提高了车身33%的刚性,而铝合金在整个白车身中占比最大,达到58%,至于只占0.5%的镁合金就主要集中在发动机舱的三角架中,此材料的应用比上代车型减重28%,其余40.5%则是钢或超高强度钢。
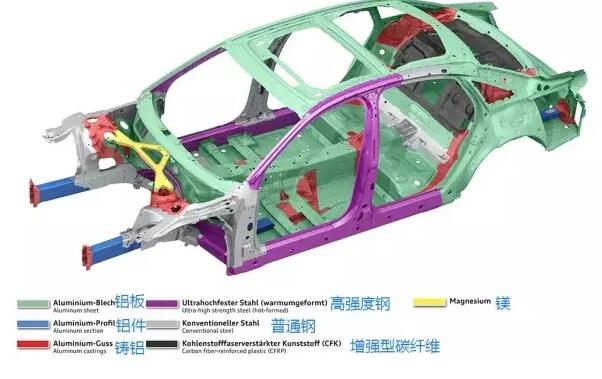
镁合金神奇吗?
对于新一代奥迪A8而言,属于新技术的可能就是采用了镁合金。这个镁合金的部件,它的位置处于发动机舱的位置,类似“顶吧”的作用。奥迪工程师表示,这个镁合金的支撑杆能够降低28%的重量!
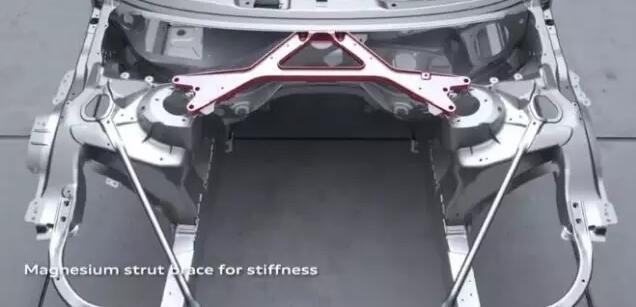
镁金属的1.738g/cm³,而铝的密度为2.702g/cm³,镁合金相比铝合金材质能够降低大概20%-30%重量。与此同时,这个部件是采用铝合金螺栓固定在支柱塔顶上。
CFRP的材料主要使用在后排座椅的背板上,相比现款的铝合金材料,重量减轻了50%,而此背板的技术含量也是最高的,奥迪称之为增强型碳纤维复合材料,最受力的地方由19层材料组成,并且以不同的编制方向缝制,无论来自纵向还是横向,甚至剪力都有极佳的抵抗效果。至于为何要在背板上下如此大功夫?首先这是一辆旗舰车型,坐在后排的才是老板,其二,它还得要肩负保护电池的作用。
全系一代A8居然比上代还重!
科技含量这么高,全新一代A8居然比上代还重?第二代A8的白车身重量为249kg,第三代为215kg,第四代为231kg,全新一代重量达到282kg,居然比上代重了51kg。重的原因是,这代A8将面临着一个动力变革的时代,除了传统汽油发动机之外,48V和PHEV混合动力车型都很有可能出现在A8上,所以在车架上必须预留了安装锂电池的位置,并且针对电池系统进行了更为坚固的力学设计以满足最高级的碰撞测试需求。在车身刚性提高24%的结果下,白车身的重量也随之增加,但根据奥迪方面表示,目前竞品的重量还未低于300kg,也就是说他们还处于领先水平。
四种材料的应用,需要14种拼接的方法
由四种材料打造的车身需要通过不同的工艺才能将他们拼合在一起,例如铝合金和铝合金之间会通过电阻点焊接、激光焊接,CFRP和铝合金需要黏合等等,而B柱里面混合着普通钢、高强度钢和铝合金板材就需要卷边和铆接的方式连接。将这些东东稳固地连接起来是一件异常复杂的事情,大概也只是有在顶级车型上使用,在全新A8上用了14种拼接方法,拆车君不敢说这是行业标杆,但起码是使出了大众集团的浑身解数。
这些复杂的拼接工艺或许对用家来说并不感兴趣,事实上,它们除了提高安全性之外,还能加大后排乘客上下车的空间。由于这种复合的连接方式,A柱、C柱都变细了,所以后门开口比上代高了14mm,宽度增加36mm,后排腿部空间也增加28mm。
生产线升级更花血本
这车身在德国内卡苏姆车厂制造的,据奥迪称制造这车身需要14道工序,需要建造41米高的车身工厂并且升级生产线,其中钢铁就用了14400吨,相当于埃菲尔铁塔的两倍用量。新车身对富豪来说是好事,就是苦了工人,因为要保证车身的品质,每个车身都有2000个检查点,而每个班组每天都会抽出一台额外检查,检查点多大6000个。